3D Printing vs CNC Machining: Which is Best for Prototyping Mould Tools?
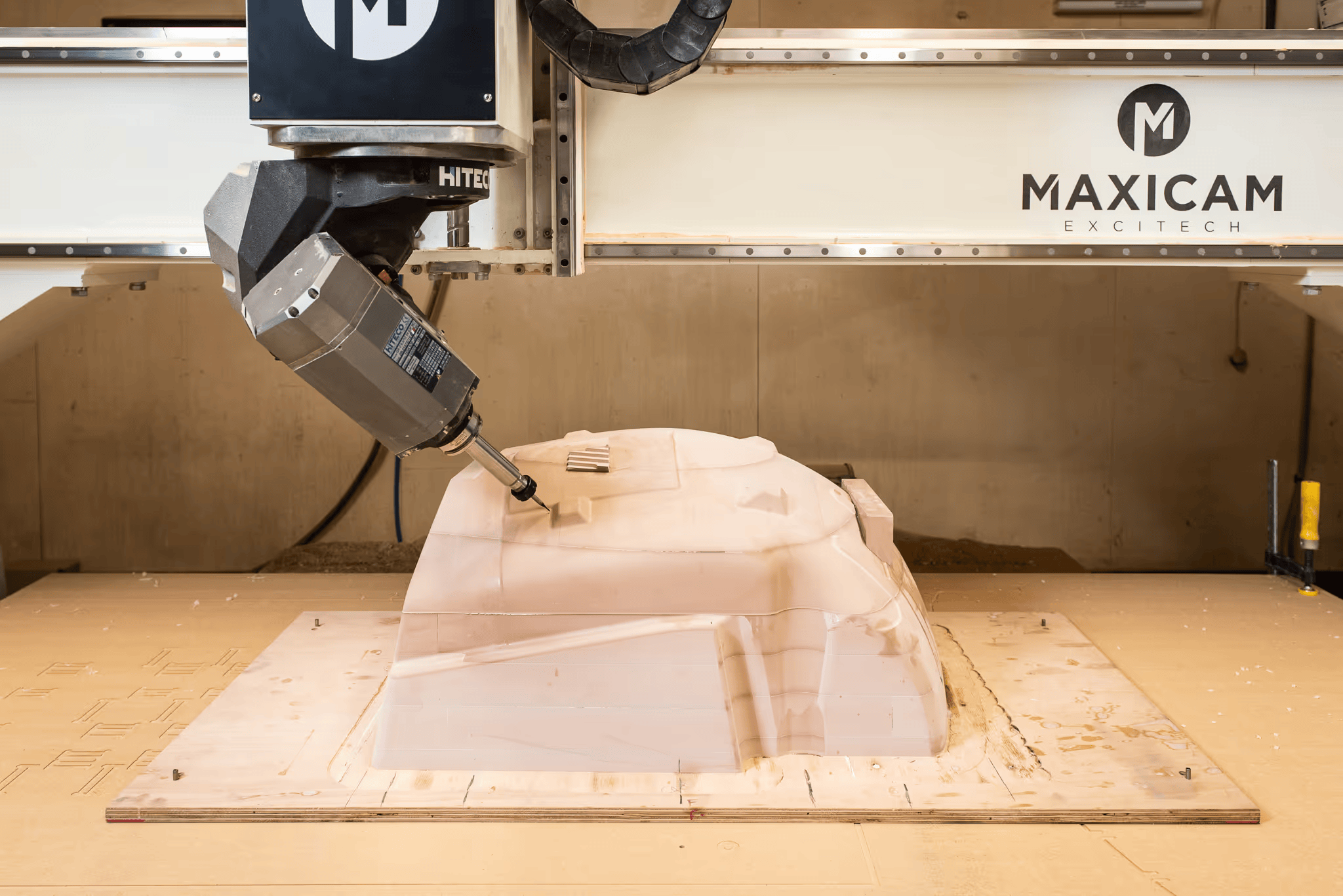
Introduction
Prototyping is a critical part of most product development processes. Back in the day before CNC machining, this would all have been done by hand. Maybe with clay, wood, or styrene foam. Then CNC came along in addition to other materials such as resin boards and changed the game. 3D printing has been the new kid on the block for some time, but has it become grown up enough to go from making one-off products to making prototype mould tools, capable of producing 50+ mouldings? We’ll take a look and find out.
Some mould tools are more equal than others
As an initial consideration, not all mould tools are created equal. Anything requiring a hot tool is simply not appropriate for non-metal tools apart from some very niche (and expensive) resin boards. For the purposes of this blog post, we’ll be assuming tooling for (comparatively) lower temperature, lower pressure processes such as vacuum forming, pressing of foams and moulding by expanding polyurethanes for example.
When choosing between CNC machining of model board (resin board) and 3D printing, it’s important to consider how each method impacts speed, cost, and material properties. Here, we’ll explore all these factors, along with the differences between FDM (Fused Deposition Modelling) and resin 3D printing, to help you choose the best solution for your tooling needs. It’s worth remembering that not all resin/model board is the same. We’ve assumed a typical density (0.7gm/cm3) polyurethane tooling board with a standard CTE.
FDM Versus Resin 3D Printing: Which is Better for Mould Tool Prototyping?
Before we can begin to compare, we need to talk about 3D printing. Within 3D printing, FDM (Fused Deposition Modelling) and resin printing each offer unique advantages and limitations for rapid prototyping. They are very different from each other, as showcased below.
- FDM Printing: FDM is widely accessible, using thermoplastic materials like PLA, ABS, and PETG. It’s cost-effective and suitable for larger, simpler parts. However, FDM prints often have visible layer lines and require post-processing to achieve smooth finishes, making it less ideal for applications needing high surface quality or intricate details.
- Resin Printing: Resin 3D printing, such as SLA (Stereolithography) or DLP (Digital Light Processing), offers finer detail and smoother finishes straight off the printer. It is well-suited for intricate designs and smaller prototypes. However, resin printing is generally slower than FDM for larger models and is more expensive, particularly when using specialty resins designed for heat resistance or durability. If something is detailed and flat, then resin is a great choice. As prints get taller, the time increases exponentially.
For anything requiring surface finish, like a vacuum forming, resin will almost always be the way to within the 3D printing family.
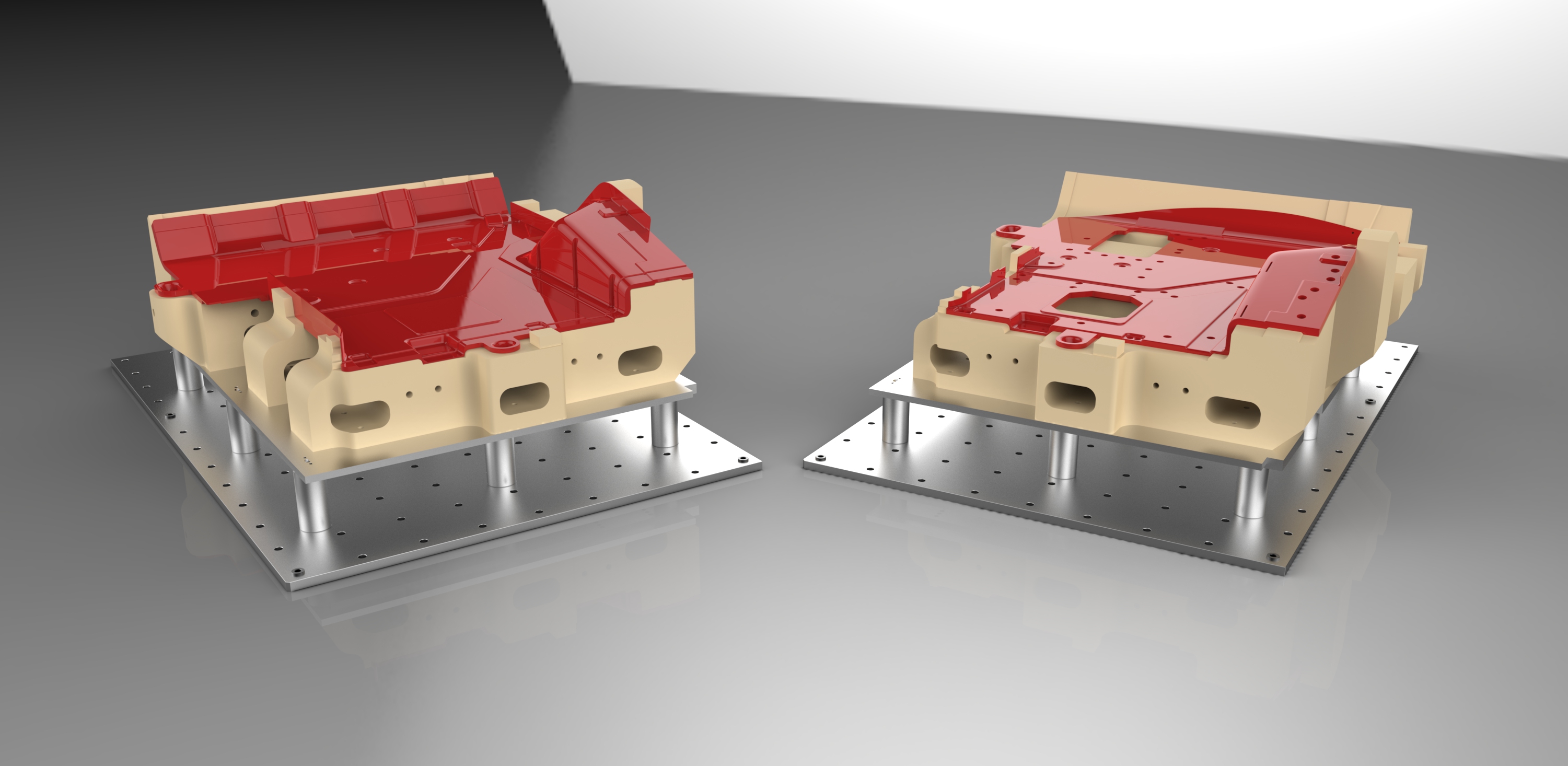
Speed: 3D Printing vs. CNC Machining Model Board Prototypes
3D printing sometimes offer faster turnaround times than CNC machining. Crucially it can also be manufactured by operators with less technical training and the costs of something going wrong is much lower. In a few hours of training, someone with no prior knowledge can print a mould tool that is pretty passable.
If a tool is relatively small then 3D printing can be a great option, particularly if you don’t have a large bank of CNC machines waiting to turnaround prototypes quickly. If the mould tool is large, then there can be significant material cost savings with 3D printing but that could be more than offset by the time it takes to produce the tool.
For anything larger, CNC machining of model board (resin board) is still highly efficient and is often faster than working with 3D printing. The edge detail that model board can hold without breaking down under pressure/heat is significant and the surface finish is greater in many cases.
Size and Cost: How Tooling Dimensions Affect 3D Printing Costs
The size of the tooling directly impacts the cost of 3D printing. Larger tools require more material, time, and larger printers, which increases expenses. FDM printing can be more cost-effective for larger prototypes, as it’s faster and cheaper per volume than resin printing. Real care though needs to be taken with the internal structure of the print to prevent collapse under pressure. Generally, as tools get larger and more complex, CNC machining model board often becomes more cost-efficient and scalable, particularly for applications like vacuum forming and press tooling.
Materials and Surface Finish: CNC Machining Model Board vs. 3D Printing
When it comes to surface finish, model board machining and resin 3D printing both offer smooth results. Model board machining provides a consistent finish without visible layers if laminated correctly, which is ideal for mould tools. FDM, by contrast, requires more post-processing to achieve comparable smoothness.
Detailing Capabilities: Precision and Accuracy in Model Board CNC Machining
For high-detail designs, CNC machining of model board offers excellent precision and can achieve tight tolerances, making it suitable for more tooling applications. Resin printing also provides high-detail capability and is comparable in precision, but it is generally limited to smaller parts and more intricate geometries. For very tight tolerances, such as holes or pins, CNC machining will be preferred as even with model board you should still be able to hold a tolerance of 0.05mm whereas with resin printing that would be about 0.2mm.
FDM printing is less suitable for applications requiring fine detail or tight tolerances due to its layer-based process and lower resolution.
Heat Resistance and Durability: Model Board vs. 3D Printing Materials
Model board’s heat resistance is far superior to that of most 3D printing materials, especially FDM thermoplastics, which are generally unsuitable for high-temperature applications. High-temperature resins exist for resin printing, but they come at a higher cost and still lack the durability of CNC-machined model board.
Model board’s thermal stability and resilience make it the preferred choice for prototyping tools used in vacuum forming and other processes where heat is needed. It should be noted though that model board is by no means always the solution. With shallow flat tools for example model board will struggle in the vacuum forming process for any longer duration of use, often bowing up / distorting.
The Verdict
The technology just isn’t there yet for the 3D printing of large prototype mould tools. It will come in time, but for now it hasn’t. For anything above approximately the size of an A4 paper footprint, the CNC machining of resin board is the winner. It currently wins on flexural strength, compression strength, hardness, temperature resistance and low CTE (essentially, expansion under heat).
That said, the technology is improving all the time. For extremely low-pressure processes, or where surface finish isn’t important (such as working with foam) then FDM printing may be more attractive. Equally for flat, detailed mould tools needing surface finish, resin printing can be used very effectively.
DPS Designs: Your partner for prototyping
Thankfully for customers, DPS Designs has the capacity and capability for both DFM/resin 3D printing and rapid prototyping in all resin boards. Whatever the project, we have something to suit you. We manufacture around 1,000 mould tools and fixtures every year across aerospace, automotive, confectionery, off-highway and medical industries.
Get in touch if you’d like us to help you with your next project.